FAQ
Oft erreichen uns Fragen unserer Kunden und Vertriebspartner rund um den Kondensator, welche allgemeingültige Themen berühren und durchaus für andere interessant sein können. Daher machen wir unsere Kommentare dazu an dieser Stelle für jedermann zugänglich.
The major part of ELECTRONICON’s range of cylindrical power electronics and power factor correction capacitors in metal housing with internal safety mechanism has been successfully approved by UL to the American UL810 capacitor standard as well as to the Canadian CSA 22.2 standard earlier this year. The maximum voltage rating which can be tested by UL is limited to 1200Vrms for oil-filled capacitors, and 1000Vrms for gas-filled capacitors. Our oil-filled capacitors with plastic lid have been tested and approved for voltage ratings of up to 660Vrms.
The UL approval procedure has been carried out by construction design, materials and testing of the safety device. Under UL rules, the capacitors are classified for approval by their design features.
Most of ELECTRONICON’s AC capacitor ranges are classified by applications rather than by design. Hence the classification for UL approved AC capacitors is not done by ELECTRONICON’s part numbers, but by a group denomination which includes all approved designs as follows:
- MKP for all three-phase capacitors with metal can, metal lid, and internal Break Action Mechanism, filled either with gas or with oil. This includes ELECTRONICON part ranges E62-3ph, 275, 276, 277, 278 and 280, terminal designs K, L, M, and S.
- MKP-1 for all single-phase capacitors with metal can, metal lid, and internal Break Action Mechanism, filled either with gas or with oil. This includes ELECTRONICON part ranges E62, E65, 275, 276, 277, 278 and 280, terminal designs C2, C6, K, L, M, and S.
- MKP-1 for all single-phase capacitors with metal can, plastic lid, and internal Break Action Mechanism, filled with oil. This includes ELECTRONICON part ranges E62, 276, terminal designs D1, D2 and G1.
As regards the mounting position of our capacitors, our Mounting Instructions state the following: “MKP capacitors with liquid or viscous filling shall be installed upright with terminals facing upwards. Please consult our technical department if different mounting position is required. Capacitors with gas or solid resin filling can be mounted in any position without restriction.”
This statement is related to the electrical operation of our capacitors only and does not concern transportation or storage. Even after very long storage or transportation in horizontal position, gravity will cause the liquid inside the capacitor to restore its original position within minutes after the capacitor has been put into vertical position again.
It is therefore safe to transport or store ELECTRONICON capacitors with oil filling in horizontal position.
Yes. All capacitors currently manufactured and supplied by ELECTRONICON, including their component parts, comply with the requirements of the regulations listed below:
- Art. 4 of Directive 2011/65/EU of the European Parliament and of the Council of 8 June 2011 on the restriction of the use of certain hazardous substances in electrical and electronic equipment (RoHS recast) except those application(s) exempted by Annex III or Annex IV of 2011/65/EU and respective Commission Decisions
- Art. 4 (2) of Directive 2000/53/EC the European Parliament and of the Council of 18. September 2000 on end-of life vehicles except those application(s) exempted by Annex II.
- REGULATION (EC) No 1907/2006 OF THE EUROPEAN PARLIAMENT AND OF THE COUNCIL of 18 December 2006 concerning the Registration, Evaluation, Authorisation and Restriction of Chemicals (REACH), Title VIII, Annex XVII), including the Candidate list of Substances of Very High Concern (“SVHC”).
We are not using SVHC in our products.
With each purchase order, our suppliers of materials, compounds or compositions are prompted to abide by the a.m. directives and prohibitions of use and require their sub-suppliers and sub-contractors to do so as well.
The application of any substances which are subject to RoHS/REACH/SVHC must be advised by our supplier before supplying the affected materials.
Unlike electrolytic capacitors, our E62 series capacitors in MKP technology (metallized polypropylene, dry or oil-immersed system, hermetically sealed metal case) do not have a limited shelf life. Even after many years of storage, these capacitors are still in their original state and can be used without any need for pre-treatment, forming, or anything else. The castor oil which our capacitors are filled with is long-term stable and not subject to any deterioration over time.After long term storage, capacitors with oil-filling should undergo a visual check for external damage, or eventual oil-leakage in order to avoid any trouble from penetration of oxygene or humidity. Other than that, not testing or measuring is necessary.Our warehouse is working on the FIFO (first in, first out) principle to ensure short storage periods for our articles. However in our broad range of very specialized capacitors for power electronics, it happens that capacitors are used only sporadically, i.e. ordered only once in two years or even longer periods of time. Hence it is possible that customers’ orders are served with a mix of capacitors originating from various periods.We wish to point out that there is no reason whatsoever to assume any deterioration of quality in such products. In fact, all of ELECTRONICON’s warranty terms are based on the date of invoice, not the date of manufacture.
ELECTRONICON Kondensatoren GmbH (EKG) is aware of the conflict and the violations of human rights in the conflict area of the Democratic Republic of Congo (DRC), and the fact that tin as applied in electronics and electrotechnics, which has been mined in the DRC is used to finance this on-going disastrous conflict.EKG has adopted a due diligence policy designed to prevent our supply chain from using conflict minerals originating in the DRC. Our tin suppliers have been required to pay attention to this matter. All tin suppliers have confirmed that in their supply chain they avoid any usage of materials from the conflict area.It is our goal to provide complete transparency of our supply chain to our customers. Moreover we are working to develop and implement a comprehensive supplier approval system to support our policy of transparency and help us insure that EKG does not contribute in whatever form to such conflicts.
Unless requested otherwise by our customers, the test voltages for our power capacitors are based on standards EN IEC 61071 (PEC) or EN IEC 60831 (PFC). Further, we have to ensure compliance with UL810 for all capacitor ranges which have been approved to the UL810 standard.
1. TEST VOLTAGE BETWEEN TERMINALS
Single-phase PEC:
- AC-capacitors: Testing is permitted with AC or DC voltage. Which method is used depends on the available testing equipment per production department and voltage range.
- If the testing is done with alternating voltage, then it is carried out with an rms-voltage which is 1.5 times the value of the capacitor's AC rating.
- If the testing is done with DC voltage, then it is carried out with a DC voltage which is 2.15 times the value of the capacitor's AC rating.
- DC-capacitors: Testing is carried out with DC voltage.
- DC capacitors are tested with 1.5 x rated UNDC
Note that thanks to special metallization, the majority of our E62 and E53 capacitors as well as many items of the E51 and E59 series have a DC rating which is substantially higher than their AC peak value. In these cases, the test voltage is referred to the DC voltage and the capacitor is tested in accordance with that voltage, i.e. 1.5 x UNDC.
Three-phase PEC:
In general, the same rules apply in accordance with IEC 61071. Our three-phase AC-capacitors are always tested with an AC-voltage. The test voltage between terminals UTT for three phase E62/E65-capacitors is usually calculated as UTT = Urms x 2.15. This is marginally higher than an rms-voltage calculated as 1.5 x UNAC.
2. TEST VOLTAGE BETWEEN TERMINALS AND CASE
The test between terminals and case is always carried out with an rms-voltage.
- According to IEC 61071 (PEC), the test voltage is calculated as 2 x UN + 1000V, but to be 2000V as a minimum.
- The rule „1000V + 2 x UN“ is stated as well by standard UL810 for all AC capacitors, however without the minimum requirement of 2000V.
- According to IEC 60831 (PFC), the test voltage is calculated as 2 x UN + 2000V, but to be 3000V as a minimum.
- For the sake of simplification of our processes, we therefore always test with at least 3000V.
3. DURATION OF TESTS
In accordance with both standards, all of the above tests are to be applied for a duration of 10s for routine testing.
- In type tests, we apply all test voltages for 60s (or longer if agreed with the customer).
Both standards allow for the reduction of testing time for the sake of production efficiency: capacitors may be tested with a period of 2s at calculated test voltage +10% (IEC 61071) or +20% (IEC 60831).
- For our DC capacitors, we apply the rules of IEC 61071 (2 sec at +10%).
- For the sake of simplification of our processes, our AC capacitors are always tested in compliance with the tougher of both standards (IEC60831), i.e. 2 sec at +20%.
The data which are essential for the quality of a capacitor, are:
- capacitance
- loss factor (which is depending on frequency!!)
- series resistance (which, as we have explained in other documents, cannot be measured correctly)
Any of the three depend on the same kind of measurements:
If using a universal low-signal measuring bridge, the bridge works with a four-point-measurement method: current is created by two separate points at the „Device Under Test (DUT)“, and voltage is measured by two different separate points. The universal measuring bridge compares the corresponding phase position between the voltage and current readings and computes the three values listed above from these readings. Such Four-point-measurement can at least neutralize, to a big extent, the distorsions caused by the measuring cables.
Please mind that MKP power capacitors have a very low series resistance and very low loss factor by their nature; hence such measurements with low-signal measuring devices are always difficult and always include plenty of potential for reading errors and distorsions. No matter which of the values are read, they always include the risk of reading errors, and again there will be rather big variation of the values.
In type tests, we use calibrated high precision instruments, e.g. TETTEX measuring bridge. But note that these are NOT low-signal measuring bridges! But even these devices bear the risk of reading errors.
If the customer insists, it would be a possible option to measure some of the capacitors with such a high precision device at mains frequency. However, we have to point out that we DO NOT MEASURE all our capacitors in series production with high precision laboratory instruments. That is impossible in regular production. For our production routine tests, we use a small-signal measuring bridge type AGILENT 4263B at 100Hz. However, in our regular production, we consider all capacitors “passed” which stay within a defined limit level. For some customers and “their” capacitors, we issue general test reports on their request which list the limit values for the customer’s reference.
We understand the requirement of our customers to have some measurement at hand which would be able to prove that the capacitors are in good order. However both the measurement of the key features series resistance and loss factor tanδ are not possible with reasonable technical means; we must acknowledge that it does not give sufficiently exact results with commonly available equipment.
The rough measurement following our practice of threshold values may give certain assurance, however it also bears the risk of measurement errors and may be misleading again.
Since 1st December 2013, all standard newly manufactured ELECTRONICON capacitors of the PFC and Power Electronics ranges which are routine-checked on test rigs with integrated labeling facilities have been provided with a modified data matrix code. This modification may not refer to certain capacitors with bespoke labeling.
In particular, the following parts are marked with the matrix code:
- all capacitors from series 275…280 except terminal design “D”
- all capacitors from series E50, E53, E55
- all capacitors from series E62, E63 and E65 which are labeled with a sticker (as a rule, this are all capacitors with diameter ≥45mm and can height ≥85mm)
- parts of the E51 and E54 series
The extended matrix code is composed in the DATAMATRIX ECC 200 standard and can be scanned and utilized by the user as well. It allows for complete product traceability by means of biunique identification of
- the test results (9…12 digit test ID)
- the manufacturing batch (9 digit production order no.)
- the product code (12…18 digit ELECTRONICON product code without “.” and “-“)
The three ID numbers are encoded in the above sequence and separated from each other by a hash sign (“#”). They are not displayed as clear text on the capacitor label.
Module width on 60x45mm labels: 5 points
Module width on 100x65mm labels: 7 points
We are convinced that this extension enhances the safety of our processes and is in the best interest of our customers. Please note that capacitors manufactured prior to 1st December, 2013, as well as capacitors NOT tested on test rigs with integrated labeling facility may not contain the extended code as described above.
All AC capacitors with metal can manufactured by ELECTRONICON contain a failsafe device as standard for protection against overload and failure at the end of service life. It is called “Break Action Mechanism” (BAM).
Functioning of the Break Action Mechanism:
In the event of overvoltage or thermal overload or ageing at the end of the capacitor‘s useful service life, an increasing number of self-healing breakdowns may result in a non-healing breakdown. This will provoke rise of heat in the vicinity of the breakdown spot and cause rising pressure inside the capacitor. To prevent it from bursting, the capacitor is fitted with an obligatory «break action mechanism» which is based on an attenuated spot at one, two, or all of the connecting wires (depending on the design and electrical function of the product) inside the case. With rising pressure, the case begins to expand, mainly by pushing the lid upwards. As a result, the prepared connecting wires are separated at the attenuated spot, and the current path is interrupted irreversibly.
The proper and flawless functioning of the capacitor safety device is standard part of every internal and external type test under applicable standards IEC61071, IEC60831, IEC/EN61048, IEC/EN60252-1, UL810 and UL840 and has been verified by our R&D many times. It has also been tested and verified as part of the capacitor approval procedures by independent certification institutes, such as UL (USA) and VDE (Germany).Note:Please mind that this safety system can act properly only within the permitted limits of loads and overloads. Under conditions of excessive operating temperature, heavy harmonic resonances, continuous heavy overcurrent, or substantial overvoltage, the stability of the polypropylene dielectric may be impaired to such extent that controlled self-healing is no longer possible, and internal insulation may be impaired.
In such events, the rise of pressure can happen with such speed and power that the break action mechanism has no opportunity to disconnect the capacitor safely. Further, the safety mechanism may not act properly if blocked from proper expansion by cables, brackets or other mechanical obstacles.
Additional means of precaution:
Capacitors consist mainly of polypropylene (up to 90%), i.e. their energy content is relatively high. They may rupture and ignite as a result of internal faults or external overload (e.g. temperature, over-voltage, harmonic distortion). It must therefore be ensured, by appropriate measures, that they do not form any hazard to their environment in the event of failure or malfunction of the safety mechanism.
ELECTRONICON is manufacturing capacitors in rectangular cases for power electronics and for medium voltage power factor correction.
Outward parts and materials:
- The cases of our E56/E59 capacitors are made of either stainless non-magnetic steel, or aluminium. As a rule, they are sealed hermetically by a welded lid of stainless non-magnetic steel, or aluminium respectively.
- In some models, the terminal side of the capacitors is not sealed by a welded lid but covered by a special resin compound to offer outward UL94-V0 conformance. The outward cover resin used in such capacitors is listed by UL (UL-File E108835). More details are available on request if applicable.
Other outward parts of the capacitors comprise
- tinned brass terminals with insulators made of FRIANYL polyamide (UL94-V0)
- steel or aluminium mounting brackets (non-flammable)
- (optional) pressure signalizer made of stainless steel/brass (non-flammable)
Internal parts and materials:
- When discussing the flammability or fire hazard of capacitors it must be noted that, to its major part, any modern power capacitor contains metallized polypropylene film which forms the “dielectric and plates” of the capacitor. No matter which capacitor manufacturer or supplier of the applied film, the polypropylene is always flammable. Hence film capacitors always contain a substantial amount of fire load. Anyone who claims that all internal parts of his capacitor are flame-retardant, or non-flammable, is either incompetent, or trying to fool the customer.
Other internal parts comprise:
- polyurethane resin used for the internal filling of all our box-type capacitors; it has successfully passed glow wire tests in conformance with DIN IEC 60695-2-13. The details of the tests are listed in the attached test report by the accredited laboratory of Ostthueringische Materialpruefungsgesellschaft fuer Textil und Kunststoffe mbH. For all potting resins used by ELECTRONICON, a glow wire ignition temperature (GWIT) of >775°C was established and confirmed. All tests were passed without ignition acc. to IEC 60695-2-13; for details, see annexed file Test report OTMG on potting resins.pdf
- internal polycarbonate insulation (depending on capacitor type; used, for example, for PD-free capacitor construction in HVDC applications and in MSD medium voltage capacitors): Glow wire flammability index (GWFI) 960°C acc. to IEC 60695-2-12; for details, see annexed file Makrolon PC_Datenblatt.pdf
- internal insulation compound “Polytrix” (depending on capacitor type): rated Class B - 130°C acc.to IEC 626-3/100-102-115; details are available on request if applicable
- copper wires and bus bars for internal connection of the capacitor sections (non-flammable)
- zinc of the contact spray of the winding sections (non-flammable)
- solder tin (non-flammable)
It is obvious that despite the best features of non-flammability or flame retardancy, any organic material will eventually burn if heated up sufficiently and long enough. The fire load stated in our data sheets and catalogues is therefore an information which enables the user to evaluate the potential for energy set free in the event of a fire and complete combustion of the described product, no matter whether originating from external or internal sources.
Based on our experience and calculations, the average fire load in polypropylene capacitors is estimated to be approx. 40 Megajoule per kilogram of capacitor weight. This estimation is in line with the official statement issued by the “Workgroup Power Capacitors” within the German ZVEI (Association of Electrical and Electronics Manufacturers) which unites Germany’s leading capacitor manufacturers, such as ELECTRONICON, EPCOS and VISHAY.
ELECTRONICON capacitors are made with highest care using top quality materials. The metals and plastics used in our capacitors are designed to sustain 25 years of operational and storage life.
When rating life time of our capacitors, however, it must be considered that, like any other electrical and mechanical component, capacitors have a certain likeliness of failures during operation. There is no part or component in the world which would have a failure rate of zero. Every engineer knows that in reality, it is impossible to predict the exact time of failure of a component. It may (and DOES) happen, that a component fails very soon after start of operation, whilst other may run many times longer than rated.
The likeliness of failures is measured as “FIT”, Failures In Time. The FIT rate makes no statements about the moment of failure, it only gives an estimation of the numbers of failures to be expected over a defined period of time.
While the mechanical FIT rate is negligibly low, the electrical FIT rate of our capacitors depends mainly on the nature and amount of the operating voltage, and the temperature:
- if our cylindrical DC capacitors (e.g. PK16™ range) are operated at a hotspot temperature of no more than 70°C, and with no more than their rated voltage, then the FIT rate is below 50 FIT, this is equivalent to a failure rate of <0.5% during 100,000 hours.
- if our cylindrical AC capacitors (e.g. E62- and E62-3ph-series) are operated at a hotspot temperature of no more than 70°C, and with no more than their rated voltage, then the FIT rate is below 100 FIT, this is equivalent to a failure rate of <1% during 100,000 hours
- if our large size, box-type DC or AC capacitors (e.g. E56 and E59 series) are operated at a hotspot temperature of no more than the value stated in the data sheet, and with no more than their rated voltage, then the FIT rate is below 300 FIT, this is equivalent to a failure rate of <3% during 100,000 hours
Assuming an average usage of 10 hours/d, this period of 100,000 hours would cover a time of 10,000 days = 27.4 years. Assuming 12 hours/d, this period would cover 23 years.
ELECTRONICON committed to making realistic statements only. We do not promise things which we cannot keep or prove. That’s why, our FIT statements are related to a realistic operating cycle of 100,000 hours.
Due to ageing processes of the materials, the FIT rate may rise after the first period of 100,000 hours. Depending on the operating conditions of the customer, there will be more or less items which can fail during this period.
Capacitors have a tolerance band because the film (which is of very fine thickness) may have some tolerances. The capacitance depends, among other things, very strongly on the DISTANCE between the capacitor plates (the closer, the higher). The slightest deviation of film thickness does have an impact on the capacitance. We can (and do) counter that by adjusting the area of film wound into the bobbin, however there are limits. Also, there is always a certain shift of C during the manufacturing process (heat treatment when the film shrinks, which causes additional change of C). It is therefore normal to have a capacitance tolerance of +/-10%. The user is supposed to consider that, i.e. calculate with the worst case scenario.
We are able to observe a tolerance band of +/-5% without additional cost. If a customer requires a more narrow tolerance band, then we have to pre-select the components, i.e. more items will “fail” the test for falling out of the tolerance band. That has an impact on the total cost of the batch.
ELECTRONICON Kondensatoren GmbH (former RFT Kondensatorenwerk Gera) have been associated with the manufacture of capacitors in Gera since the late 1930s, when the SIEMENS organisation moved part of their production facility from Berlin to eastern Thuringia in the heart of Germany.
Since then, the company has extended considerably. Highest quality and reliability of all products have been the core of our philosophy from the very start. Continual development in its product ranges has resulted in ELECTRONICON becoming one of Europe's leading capacitor manufacturers supplying customers worldwide.
The company employs about four hundred and fifty qualified engineers and skilled workers in its manufacturing facilities, producing capacitors for lighting, motor, and power electronics applications, further components, modules and capacitor banks for power factor correction.
Regular investment in advanced and environmentally sound technologies guarantees the highest level in manufacture and quality to modern standards which are approved by standard authorities all over the world.
ELECTRONICON’s ranges of power capacitors for applications in power factor correction and harmonic filtering have been tested and approved by the German VDE as well as by the American UL Institute in order to prove accordance with relevant IEC and UL/CSA standards and suitability for use in contemporary industrial applications.
As is common practice with international standard institutions, the approval of product ranges is done by evaluating and testing representative specimen which are considered the most critical within their range. The UL institute decided to test 1200V capacitors for MKP and 1000V which represented the highest voltage stress and were representative in terms of reactive power and current.
Both standards UL810 as well as CSA 22.2 focus on the safety of capacitors. Very high attention and extensive testing are therefore dedicated to the verification of safe failure mode and secure operation of the capacitors. The requirements by these two standards exceed the IEC clauses substantially. In the case of VDE, our focus at the time was on verifying the voltage ranges of 400 to 525V. Hence there the 40kvar 525V capacitor was tested as the representative with the highest stress and reactive power. It has to be noted that, whilst UL/CSA-approval marks are obligatory for sales in the respective countries, a mark of VDE or any other European standard institution is not obligatory for power capacitors. Therefore, the type test of 40kvar 525V was made on agreement between ELECTRONICON and VDE as a voluntary test. The type test by VDE was fully based on the provisions of IEC60831 (2003) parts 1 and 2.
What is the failure mode of box type capacitors under over voltage, short circuit, thermal overload?
Under conditions of strong overload (e.g. excessive temperature, permanent overvoltage), non-healing breakdowns in the dielectric may cause local overheating and disintegration of the polypropylene in the faulty spot. As a result, the pressure will raise inside the case.
ELECTRONICON has good experience with protecting box type capacitors by pressure sensors. The pressure sensor is a signaling device which monitors the internal pressure of the capacitor. As soon as a certain threshold value is exceeded, the switch in the sensor closes (or opens, depending on the customer’s preference). Usually, this threshold is set to 0.5 or 1 bar of pressure rise (depending on customer’s preference). This way, the user as an information which he now can (and must) use for external safety measures (emergency switch-off). We always offer the pressure switch option as standard in our data sheets.
If a capacitor is NOT protected by a pressure switch, the pressure will keep on rising inside the case until
- the electrical connection of the affected winding section inside the case becomes “disconnected” by the overall disintegration inside the section. Then this capacitor section will be “dead”, but the rest of the capacitor is still operating. From outside, such capacitors will look “inflated, i.e. the inside pressure has bulged out the case walls. This is happening quite often in our destruction tests, however there is no guarantee for that !
- it can no longer be withheld and the case cracks open or the terminals become unhermetical; medium size capacitors have been tested for up to 8 atmospheres (8bar) to withhold the pressure. Smaller capacitors will withhold even higher pressure, bigger sizes may become unhermetical at lower pressure.
The usage of segmented film as suggested by several manufacturers is NOT a safe alternative to the pressure switch. Segmented film does not give reliable protection in case of thermal overload, and the risk of explosion still exists. In addition to that, the segmentation causes higher power losses, fast loss of capacitance, and creates problems during heavy surge currents. Therefore, ELECTRONICON abandoned segmented technology around 12 years ago and looked for alternatives of protection.
The flashing point of polypropylene is below 200°C. (The flash point of a material describes the lowest temperature at which a flammable mix of material steam and air may create above the surface of the material. If the volume of the mix is sufficiently large, it can explode if ignited by an external source.)
The thermal disintegration of PP starts at around 300…320°C.
The ignition temperature of PP is around 330°C. (The ignition temperature – also called ignition point, self-ignition temperature) ist he temperature which the material must be heated up to in the presence of air, in order to ignite it simply by ist temperature, without external ignition.
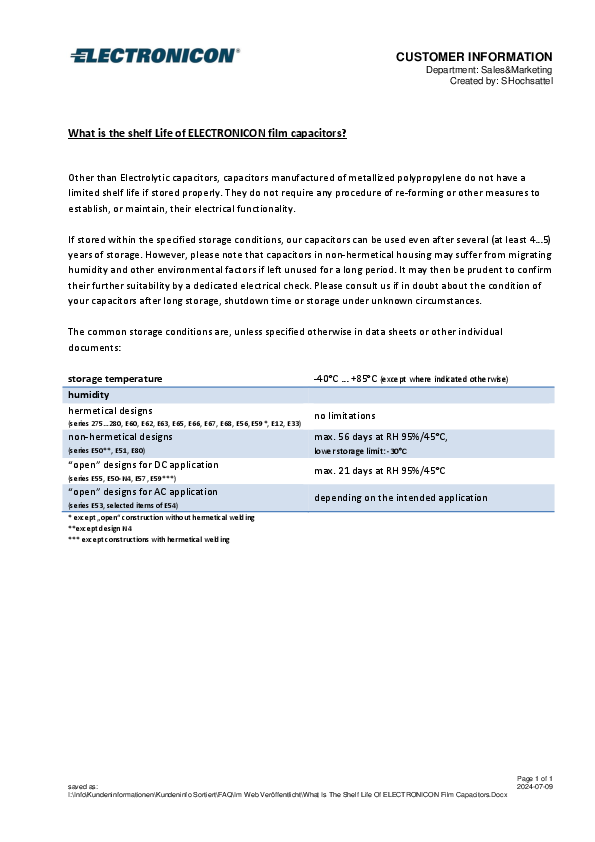
Other than Electrolytic capacitors, capacitors manufactured of metallized polypropylene do not have a limited shelf life if stored properly. They do not require any procedure of re-forming or other measures to establish, or maintain, their electrical functionality.
If stored within the specified storage conditions, our capacitors can be used even after several (at least 4…5) years of storage. However, please note that capacitors in non-hermetical housing may suffer from migrating humidity and other environmental factors if left unused for a long period. It may then be prudent to confirm their further suitability by a dedicated electrical check. Please consult us if in doubt about the condition of your capacitors after long storage, shutdown time or storage under unknown circumstances.
Documents required under European Regulations for the application for export permission at BAFA (German export control authority)
Due to their high energy field strength, certain capacitors manufactured by ELECTRONICON are regarded as Dual Use Goods as per European Export Control regulations. Whenever this applies, ELECTRONICON places a special remark in bold letters about export control liability of the affected item on the capacitor data sheet, as well as on all official documents (order confirmations, delivery notes, invoices).
According the most recent status of the regulations, European customers do not have to submit any additional documents to the supplier. If later, however, the goods are forwarded by our customers to a country outside the European Union, they must apply for the necessary export permission on their own behalf.
ELECTRONICON is committed to providing the best possible service to its sales partners and customers, and to maintain the highest possible level of customer satisfaction. One of the very important tasks serving that goal is proper packing and transportation of our products which must arrive at their destination completely and unharmed.
With thousands of shipments dispatched every year, occasional damage to the goods or their packaging caused by external mechanical, climatic or other impact is unavoidable. In order to secure your rights and respect your interests as our customer, it is necessary that you observe the following basic rules upon goods receipt and disclosure of transportation damage:
- Conduct a thorough visual inspection of the goods in presence of the delivering freight forwarder (driver) and report any damage or loss immediately on the consignment note.
- Any pallets* dispatched by ELECTRONICON are stretched in PP-foil and sealed with special tape bearing the ELECTRONICON logo. Please conduct an enforced check of the contents of your shipment if the original wrapping has been damaged, removed, or exchanged.
(*Note: this rule applies to goods packed on pallets only. Parcels are NOT wrapped and sealed this way.) - Have the forwarder’s representative (driver) sign the damage report.
- Inform ELECTRONICON immediately.
- Leave the goods and packing unchanged, do not use the goods until your claim has been accepted by the forwarding agent technical status of the damaged goods has been verified and approved.
Please note that claims referring to transportation damage not confirmed by the forwarder’s representative cannot be accepted.
Hidden damage (i.e. damage despite outwards unharmed consignment) shall be reported to the freight forwarder as well and be unpacked in his presence, for him to witness and confirm the damage. Please not that such claim must be declared within no more than one week.
Please refer to the details in our “Instructions for Handling Transportation Damage”.
We are working permanently to make our shipments safe and secure. With your continuing support, we will further strengthen and improve our logistics.
Our filter capacitors of the E62 and E65 series are not fitted with discharge resistors as standard. The applicable standard IEC61071 does not require an obligatory discharge device to be fitted to the capacitors.
Discharge resistors are required by IEC60831 standard as a means of safety to avoid health and safety hazards by electrical shock when touching the terminals of a charged capacitor. IEC60831 requires the discharge of capacitors below 75V within 3 min. However, discharge resistors which are connected in parallel with capacitors cause permanent power losses. Hence in power electronics applications, it is common to provide the discharge by non-permanent discharge resistors, or by other means.
In power factor correction, the provision of discharge resistors does also have a second purpose:
capacitors which are switched in parallel with the mains (such as PFC and three-phase Filter capacitors) should be discharged below 50V before being re-connected, in order to prevent capacitor damage by very high inrush currents if connecting a capacitor in the moment of phase opposition (i.e. a charged capacitor being switched on at the moment when the mains voltage is at the peak of the opposite voltage potential). Therefore, ELECTRONICON provides standard discharge modules for the three-phase power capacitors which are dimensioned for such discharge below 50V within less than 60 seconds. However it must be noted that these discharge modules discharge faster than required by IEC standards, and they produce higher power losses.
For three-phase filter capacitors, the discharge could be realized by
- individual discharge modules,
- a joint resistor set for a group of paralleled capacitors,
- a separate discharge unit which would be switched on only after disconnection of the capacitors.
We would recommend option one or two, depending on the circumstances. The discharge resistors could be dimensioned based on the specific requirements of the application. For that purpose, it is essential to know the total number of capacitors to be connected in parallel, and the maximum operating voltage (rms or AC value) which the capacitors may be exposed to.
ELECTRONICON’s reactors are made of high class materials, with technical focus of LOW LOSS design. As a result, the power losses of our reactor are lower than of the competition, and as a consequence, the temperature rise is lower. Hence our reactors do not get as hot as many of our competitors’ products.
Benefits:
- less waste of energy by heat losses
- less heat stress for other components in the cabinet (e.g. capacitors, contactors etc.)
Insulation class H calls for special insulating materials which can withstand this hot temperature. Since our reactors do not heat up that much, we usually design them with class B or (if customers insist in higher rating) with class F materials. This helps to reduce cost. Otherwise, with class H materials, cost would rise even though not necessary for our products.
We understand that many customers ask for class H as standard BECAUSE they are used to low quality reactors which get hot. However ELECTRONICON wishes to make a point here, since this is one of our technical advantages (lower heat dissipation means higher energy efficiency).
We normally don’t quote a lifetime because film capacitors can live very long. However everybody knows that any component (including film capacitors) may also have some failures. It is therefore silly to promise “lifetime XXXX hours”, and then receive the claim from customer that he has one capacitor which has failed after 20,000 hours. Then the customer may claim that he was not told the truth.
Therefore, we make it clear that here can ALWAYS be some percentage of failures, and we quote a FIT rate.
Our FIT rate is quoted for a period of 100,000 hours, and it is related to certain operating conditions (usually, hotspot temperature ≤70°C and operating voltage ≤rated voltage of the capacitor). This period of FIT statement is called “reference service period” and is stated in the data sheet along with the FIT rate.
Unfortunately, certain customers don’t read the data sheets carefully enough. They misunderstand the figure “reference service period” and mistake it for “lifetime”. Then they compare with competition (who often do not even explain about the FIT rate), and there they find higher figures promised as “lifetime”. As a result, the customers may decide that our capacitor is not as good as the competition.
Therefore, we have decided to make our statements more clear: we are quoting the FIT rate (which is related to the reference period 100,000 hours) AND we also make a statement about the expected lifetime. It is based on statistical experience and calculation, and it considers that due to the FIT rate, some capacitors may fail during the entire period.
Hence
- “reference service period” is NOT the statement of lifetime, it is just an explanation related to the FIT statement.
- “statistical lifetime” is the statement of lifetime; it is quite honest in making it clear that not 100% of the capacitors may still be operational at the end of the lifetime period.
Any competitor who promises a lifetime without explaining about the FIT rate is doing this based on the IEC standard rule that 3% of the capacitors are allowed to fail during the quoted lifetime. 3% corresponds to 300 FIT.
Any competitor who claims that he can guarantee 20 or 30 years operation without failure is probably lying. It must be noted that NOONE can really prove such long life by practical proof. The capacitor technology (film quality and film thickness, material composition etc.) which we are using nowadays, was not available 15 years ago. If we compare with capacitors manufactured in the 1980s or 90s, the film thickness was bigger then, the material was different, etc.
We used to quote the maximum rating of the terminals as max current rating for the capacitors. In fact, a capacitor can be operated at very high currents as long as the hotspot temperature is not exceeded, and if the ambient temperature is low enough (e.g. only 25°C), then even a very high continuous current may be possible. However, due to the rising number of applications with very high frequency currents, we then decided to limit the total current of the capacitors in our E62-3ph catalogues. We detected that under such conditions, the capacitors are not always universally suitable for the very high currents, and decided to limit the current as a matter of precaution.
Hence 104A per phase is correct as far as the terminal rating goes, but is no longer correct for the capacitor itself. The maximum current rating of the capacitors with CAPAGRIP M terminal then has become 80A only.